Supply chain and logistics executives used to joke that no one knew or understood what their jobs were — that is, until the COVID-19 pandemic upended how goods were transported to warehouses and ultimately to customers.
“Until you start to look behind the scenes, you don’t know how all of this gets to your door until you can’t get it,” says Rick Holden, vice president of business development and a corporate officer for Riverside Logistics, a Richmond-based third-party logistics and supply chain management company.
The pandemic “turned the supply chain completely on its ear” for a solid 18 months, with days of shipment backlogs and other disruptions in getting goods to customers turning to weeks and weeks turning into months, adds James Durfee, vice president of business transformation at Riverside Logistics. It was then that consumers and businesses alike had to come to terms with the new normal — that there would be significant delays and disruptions in receiving shipments at ports, finding transportation for goods, and keeping warehousing and logistics workers employed.
“As a logistics provider, we saw that our customers suddenly became much more amenable to service disruption because it became the norm, rather than the exception,” Durfee adds.
As the pandemic went on, businesses started over-ordering and overstocking goods at warehouses, which caused inventory levels to skyrocket.
“Companies weren’t really built — supply chains weren’t really built — to handle something of the magnitude of the COVID pandemic where things were shut down for huge amounts of time,” says Doug Thomas, a professor and supply chain expert with the University of Virginia’s Darden School of Business.
Across the country, inventory levels are extremely high. In the Richmond market alone, warehouse inventory levels jumped from a traditional pre-pandemic 40% to a staggering 90% by 2022. And in Hampton Roads, the warehouse vacancy rate — the amount of available storage space — is below 1%, says Trevor Dunlap, president of Chesapeake-based transportation and logistics companies Givens Transportation Solutions and Givens Inc.
Plus, the goods being stored in warehouses today are those that were in much higher demand during the pandemic that companies “mis-purchased” when people were primarily staying at home — items such as sweatpants and home goods that made people feel more comfortable in their surroundings, Holden explains. Now, amid an uncertain economy and as many companies are returning workers to offices in hybrid work models, the demand for those items is dropping.
The shift in demand “created a huge glut of inventory that we’re still working through,” he says. “Until you create more space in warehousing, you have to do something with that stuff before you can bring more [goods] in behind it.”
The logistics, warehousing, and shipping industries are now forced to regroup following this massive surge in traffic they saw during the pandemic.
“There are still pockets of stockouts and excess inventory in various industries,” says Barbara Hoopes, a professor and supply chain expert with Virginia Tech. “The shipping and logistics industries will continue to provide customers with services [like] expedited shipping and inventory controls to help stabilize these situations.”
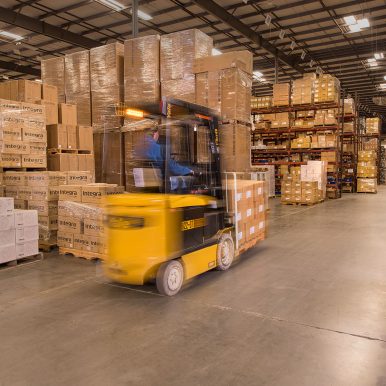
Supply imbalance, freight volumes
While much of the supply chain backlog has worked itself out, there are still challenges facing the industry, explains Mike Coleman, president and CEO of Norfolk-based logistics and shipping firms CV International Inc. and Capes Shipping Agencies. Exceedingly high inventory levels have made it increasingly difficult for companies to locate warehouses with space to store their goods.
“Everything worked its way out of the backlog in the supply chain — for the most part. There are still challenges,” Coleman says. “There’s still a lot of difficulty finding warehouse availability. Many are full with excess inventory.”
This excess inventory is what Durfee refers to as the “wrong” inventory because there is a glut of items remaining in warehouses that were popular during the pandemic, but no longer have the same amount of demand. This has resulted in Riverside Logistics having to turn down some customers or reduce the amount of space available to clients.
“We’re much more selective on who we take. We’ve actually had to ask some clients to leave our space,” Durfee says. “The nature of the beast was that we were kidding each other that we’d be a good fit long term. It took us a while to internalize that across our management team because we had never done that before.”
However, the situation is seen as largely temporary within the industry, with much of the excess inventory being sold on the discount market to move it out more quickly. In the meantime, instead of adding warehouse space, companies are turning “to leased resources [like] contracted or public warehouses for shorter-term, flexible capacity,” Hoopes says.
As warehouses reach max capacity, some logistics and warehousing companies — such as Givens — are placing a greater emphasis on hiring and retaining talent. Warehousing, distribution and logistics services continue to be in high demand as inventory levels remain high, also driving a need for industry labor, Hoopes explains.
“We definitely continue to focus on how we can be more efficient with labor,” Givens says. “On the warehousing side, we’re figuring out how we can become most efficient because that’s where our most dramatic cost increases have been over the last two years, just in wages and benefits.”
Hoopes warns, though, that increased hiring in warehousing and logistics could lead to layoffs as “needs ebb and flow.” While industry demand for labor is high at the moment, she adds, “it’s hard to say if it will last very long in the face of prolonged uncertainty.”
Thomas, of U.Va., has a more pessimistic view of how companies will handle supply chain operations moving forward.
“Mostly what I see is companies not doing too much to reshape their supply chains. I think it’s going to be forced in a few specific industries, largely due to either pressures from consumers or actions from [government] policymakers,” he says. The Biden administration has issued a couple of executive orders that have addressed reviewing supply chain capabilities and resilience across four industries deemed critical to national security and stability: food, pharmaceuticals, electronics and energy.
Changes in consumer demand
Since the surge in imports from other countries during the pandemic placed a huge strain on the logistics system, and as a result, supply chain companies are being forced to examine their future business plans. Prioritizing longer-term partnerships and retaining talent will become increasingly important in the warehousing industry as purchasing patterns stabilize so that these companies can focus on cooling consumer demand. Changes in imports from other countries have also impacted supply chain operations in the U.S.
“Spending patterns have gone back to the pre-pandemic routine. When the pandemic happened, you had people at home buying, buying, buying, and that fueled a huge spike in imports out of China and in the Far East to the United States,” Coleman says. “Now that spending patterns are going back to pre-pandemic normals, we’re seeing a major drop in container freight volumes coming to the United States from Asia.”

Ocean freight costs have come down significantly, particularly in Asia-to-U.S. trade, Coleman says, adding that in some cases rates are 75% of what they were in May 2022. For that reason, reducing freight spending is going to be the name of the game for every shipper going into the next year, he adds. During the height of the pandemic, it cost between $20,000 and $25,000 to ship a container from Asia to the East Coast, with shipping contract rates between $8,000 and $10,000 as a minimum quantity commitment, Coleman says. Now, shipping rates are below $2,000 per container, he adds.
“Shippers are anxious to recover the exorbitant rates they were paying during the pandemic, and carriers are fighting for every container,” Coleman says. “It is a buyers’ market, and carriers seem more than willing to undercut one another to the point where they are losing money. Ultimately, this is not good for shippers or the shipping industry. There needs to be stability.”
Future focused
Although the extent of the COVID-19 pandemic couldn’t have been anticipated, the Port of Virginia has actually been several steps ahead in preparing for significant changes in the shipping and logistics industries. The Port of Virginia saw record container volumes in 2022, highlighting the advantage it has in owning and operating all its terminals. Other large ports — including those in Los Angeles and New York — have multiple, competing terminal owners and operators, which means that the ports have less control over rearranging deliveries and distribution. When vessels began to back up on the West Coast during the pandemic, it was more difficult to redirect cargo, but the Port of Virginia had more flexibility.
“We can make all of the decisions necessary to accommodate these surges without any disruptions in efficiency or any disruptions to our customers and cargo owners,” says Joe Harris, spokesman for the Virginia Port Authority and the Port of Virginia. The pandemic was “a really long-term test for us, and we passed it with flying colors.”
In spring 2022, the Port of Virginia formalized a $1.4 billion capital investment project that includes expanding rail capacity, widening and deepening the channels to at least 55 feet deep and improving and modernizing equipment at the North Berth at Norfolk International Terminals. Some of the work had been announced before the pandemic, but the investment is helping the Port of Virginia build its reputation as an East Coast alternative to West Coast ports that faced massive congestion and shipping traffic jams in 2021 and 2022.
The Port of Virginia’s extensive upgrades are intended “to get ready for the next surge of cargo — whenever it may come,” Harris says. “In the port business, you must be continually investing and reinvesting in your facilities, your operating systems, your equipment. You have to look at the entire picture, and you have to have a strategy for what’s next.” Work on the projects will be complete by 2027, Harris adds.
The improvements also can be an opportunity for businesses to choose the Port of Virginia over other ports.
“There is, I think, every reason to believe that companies may start looking to source products from different places and flow them into the U.S. market through different ports,” Thomas says. “I think investment in technology, investment in the operations of the ports, is going to be important. I think that’s an opportunity for Virginia to have significant growth in the Port of Virginia.”
Tech improvements
Just as the pandemic illuminated technological inefficiencies in most industries, it also demonstrated that supply chain industries are in need of technological advancement. This is in part due to the complexity of the industry, but also labor shortages that are driving an increasing need for automation.
For example, CV International is focused on improving logistics technology because, as a freight forwarder, the company acts as a control tower for freight movement and as an aggregator for tracking data and key performance indicators related to supply chains, Coleman explains. CV International has worked to upgrade its reporting and tracking technology that can be customized for its clients to view via dashboards.
“For us, for our company, technology is huge right now — giving actionable visibility to our clients, exceptions management, cost management and an overall better managed supply chain,” he adds.
In fact, data-based decision making in supply chain industries will become “mandatory” for customers, Hoopes says. This will include technology that helps to optimize routing and scheduling as well as analytics tools to track shipments’ locations along the supply chain — particularly “shipments that are not meeting set milestones [and] that require direct attention or some extra action by our
team,” Coleman adds.
The use of artificial intelligence in the shipping and logistics industry is also beginning to be discussed, particularly in relation to the trucking industry. To combat an ongoing shortage of truck drivers, some shipping companies have been testing autonomous trucks. But Durfee and Holden point out the law still requires that a live driver be present in the autonomous vehicle, defeating the idea of the vehicles reducing labor costs.
“It’s going to take some time before we land with this,” Durfee says.